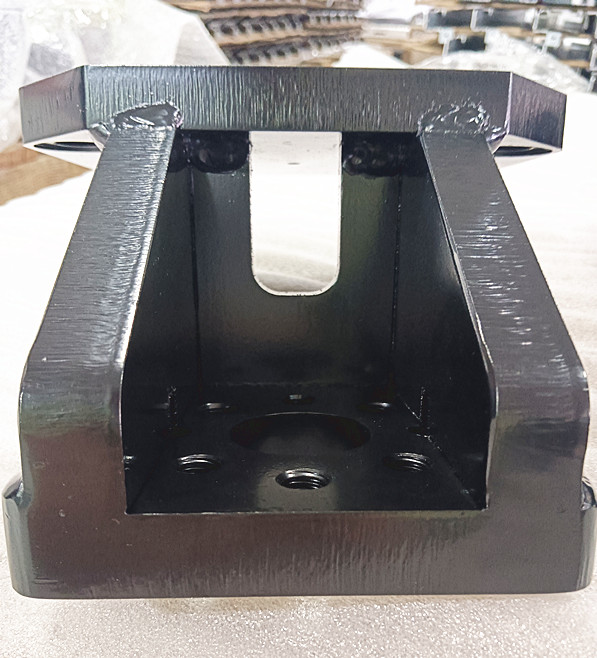
Features and Advantage of TIG welding
Tungsten Inert Gas (TIG) welding offers several advantages, making it a popular choice for various welding applications:
- High Quality Welds: TIG welding produces high-quality, precise welds with excellent control over heat input and weld pool manipulation. This makes it suitable for welding intricate joints and thin materials.
- Versatility: TIG welding can be used to weld a wide range of metals, including steel, stainless steel, aluminum, nickel alloys, copper, brass, and titanium. This versatility makes it a valuable process in industries ranging from automotive to aerospace.
- Clean Process: TIG welding uses a non-consumable tungsten electrode and inert gas shielding, resulting in clean welds free from spatter, slag, and other contaminants. This cleanliness is crucial in applications where post-weld cleaning is not feasible or desirable.
- Precise Control: TIG welding allows for precise control over welding parameters such as heat input, arc length, and welding speed. This control enables welders to produce consistent, high-quality welds, even in challenging welding positions or on thin materials.
- No Flux Required: Unlike some other welding processes such as flux-cored arc welding or shielded metal arc welding, TIG welding does not require flux, reducing the risk of weld contamination and eliminating the need for flux removal after welding.
- Low Distortion: TIG welding produces low levels of heat distortion and shrinkage in the base metal, particularly when welding thin materials. This minimizes the need for post-welding straightening or distortion correction, saving time and effort.
- Suitable for Reactive Metals: TIG welding is well-suited for welding reactive metals such as titanium and zirconium, as well as metals with high melting points like tungsten and molybdenum. The inert gas shielding protects these metals from atmospheric contamination during welding.
- Controlled Weld Pool: TIG welding allows for precise control over the size and shape of the weld pool, facilitating the welding of complex joints and the deposition of filler metal with accuracy.
- Remote Operation: TIG welding can be adapted for remote operation using robotic systems or welding manipulators, allowing for automation of welding processes in industries where consistency and precision are critical.
- Welding of Thin Materials: TIG welding is particularly well-suited for welding thin materials due to its precise control over heat input and minimal distortion. This makes it a preferred choice for applications such as sheet metal fabrication and thin-walled tubing.
Overall, TIG welding offers a combination of precision, cleanliness, versatility, and control that makes it a valuable welding process in various industries and applications.
China Sheet Metal Parts Manufacturers
China Metal Enclosure Fabrication
Sheet Metal Manufacturers in China
China Sheet Metal Fabrication Service
China Custom Sheet Metal Parts
China Sheet Metal Forming Manufacturers