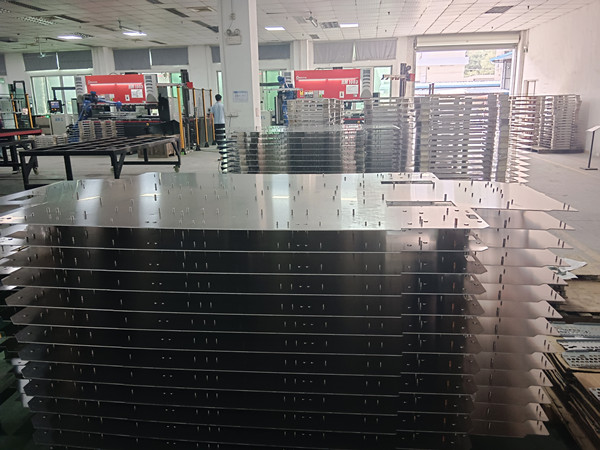
How are sheet metal parts cut?
Sheet metal cutting is a fundamental step in manufacturing, where flat metal sheets are cut into specific shapes and sizes. The cutting method depends on factors like material type, thickness, and the complexity of the design. Here are the most common techniques used to cut sheet metal:
1. Laser Cutting
- Process: A high-powered laser beam is directed at the metal sheet, which melts, burns, or vaporizes the material to make precise cuts. The laser is often controlled by a CNC (Computer Numerical Control) system to follow the design patterns.
- Advantages:
- Highly precise, capable of cutting intricate shapes.
- Minimal waste and smooth edges.
- Suitable for a wide range of materials and thicknesses.
- Limitations:
- Slower for thicker materials.
- Higher initial setup costs due to the complexity of the equipment.
2. Plasma Cutting
- Process: Plasma cutting uses a high-velocity jet of ionized gas (plasma) to cut through electrically conductive materials like steel, aluminum, and copper. The plasma torch creates an arc that melts the material, and the gas blows away the molten metal.
- Advantages:
- Faster than laser cutting for thicker materials.
- Capable of cutting conductive metals, even thick plates.
- Limitations:
- Less precise than laser cutting, with rougher edges.
- Limited to conductive materials (e.g., metals).
3. Water Jet Cutting
- Process: This method uses a high-pressure stream of water, often mixed with abrasive particles, to cut through the sheet metal. The water jet erodes the material along the cutting path without generating heat, which prevents distortion or warping.
- Advantages:
- No heat-affected zone (HAZ), so the material properties remain unchanged.
- Capable of cutting complex shapes and thick materials.
- Works on almost any material, including metals, stone, glass, and composites.
- Limitations:
- Slower than plasma or laser cutting for thin materials.
- Higher operational costs due to water and abrasives.
4. Shearing
- Process: A mechanical or hydraulic shear applies a large force to cut the metal along a straight line. It works like a giant pair of scissors, with one blade moving against a fixed blade.
- Advantages:
- Fast and efficient for straight cuts.
- Suitable for large sheets and high production rates.
- Low operating cost and simple to use.
- Limitations:
- Limited to straight-line cuts, not suitable for intricate shapes.
- May produce some deformation at the edges.
5. Punching
- Process: In punching, a die and punch are used to stamp out shapes or holes in the sheet metal. The punch forces the material into a die, shearing it off to create the desired cutout.
- Advantages:
- Efficient for repetitive patterns, such as holes and slots.
- Ideal for high-volume production.
- Can create complex patterns with the use of multiple punches.
- Limitations:
- Limited to specific shapes determined by the punch and die.
- Potential for distortion or burrs around the punched area.
6. Nibbling
- Process: Nibbling involves using a punch to make a series of overlapping small cuts along a path, creating a contour or intricate shape in the sheet metal. The nibbling tool moves in small increments to “chew” through the material.
- Advantages:
- Can produce complex shapes that would be difficult with other cutting methods.
- Works well with both straight and curved cuts.
- Limitations:
- Slower than other methods.
- May leave a rough edge that requires additional finishing.
7. Oxy-Fuel Cutting (Oxy-Acetylene)
- Process: This method uses a torch that combines oxygen and fuel gas (usually acetylene) to heat the metal to its ignition temperature. Once the metal is hot enough, a stream of oxygen is directed at it, causing the metal to burn and be blown away, making the cut.
- Advantages:
- Effective for cutting thick steel plates.
- Simple and portable equipment.
- Limitations:
- Not suitable for non-ferrous metals (like aluminum or copper).
- Generates heat, which can lead to warping or a heat-affected zone.
8. CNC Milling and Routing
- Process: CNC milling uses rotating cutting tools to remove material and create precise shapes and features on a flat sheet. CNC routers, similarly, use a high-speed cutting tool to carve out shapes from the sheet metal.
- Advantages:
- High precision for complex geometries.
- Can combine cutting and shaping in one process.
- Limitations:
- Slower than laser or plasma cutting for thin sheets.
- Typically more suited for thicker materials or detailed work.
9. Sawing
- Process: Band saws or circular saws equipped with metal-cutting blades can be used to cut sheet metal. This is more common for thicker materials or smaller jobs.
- Advantages:
- Low-cost and simple for small jobs.
- Suitable for thicker materials.
- Limitations:
- Limited to straight or curved cuts, not complex shapes.
- Slower and less precise compared to laser or plasma cutting.
Factors Influencing the Choice of Cutting Method:
- Material Type and Thickness: Certain methods are more efficient for cutting thick or thin sheets.
- Precision Requirements: Laser and water jet cutting offer the highest precision, suitable for intricate designs.
- Production Volume: Stamping and shearing are efficient for high-volume production, while laser and plasma cutting can handle smaller runs.
- Cost: Shearing and punching are cost-effective for simpler cuts, while laser and water jet cutting are more expensive but versatile.
- Edge Quality: Some methods, like laser cutting, produce smooth edges, while others, like plasma cutting, may require additional finishing.
By selecting the appropriate cutting method, manufacturers can optimize production efficiency, precision, and cost, depending on the specific requirements of the sheet metal part.
By selecting the appropriate processes and machinery, manufacturers can create sheet metal parts with high precision and quality, suitable for a wide range of applications.
Click sheet metal fabrication company china or china sheet metal forming manufacturers to learn more about sheet metal fabrication services.
For all your electrical enclosures from China, contact china sheet metal fabrication factory JIATONG now.
From Sheet Metal Fabrication Companies in China, china sheet metal fabrication manufacturers, china sheet metal fabrication companies – JIATONG
More Stories
What is the minimum distance between sheet metal bends?
The minimum distance between bends in sheet metal is important for maintaining the material's integrity and avoiding deformation or tearing...
What is sheet metal fabrication services?
A manufacturing process involving shaping and manipulating thin, flat sheets of metal, sheet metal fabrication is used to create different...
How do I choose sheet metal material?
Mechanical Factors Important to Sheet Metal Material Selection Strength, Ductility, Corrosion resistance, Ease of manufacture.etc Choosing the right sheet metal material involves...
Ways to Cut Sheet Metal Fabrication Costs
Cutting sheet metal fabrication costs involves optimizing materials, labor, and processes. Here are effective strategies to reduce costs without compromising...
What is the manufacturing industry outlook for 2025?
The global manufacturing industry is expected to experience a recovery in 2025 after a challenging 2024. Current forecasts suggest that...
What type of welding wire for sheet metal?
The type of welding wire used for sheet metal depends on the welding method, material, and thickness of the sheet....