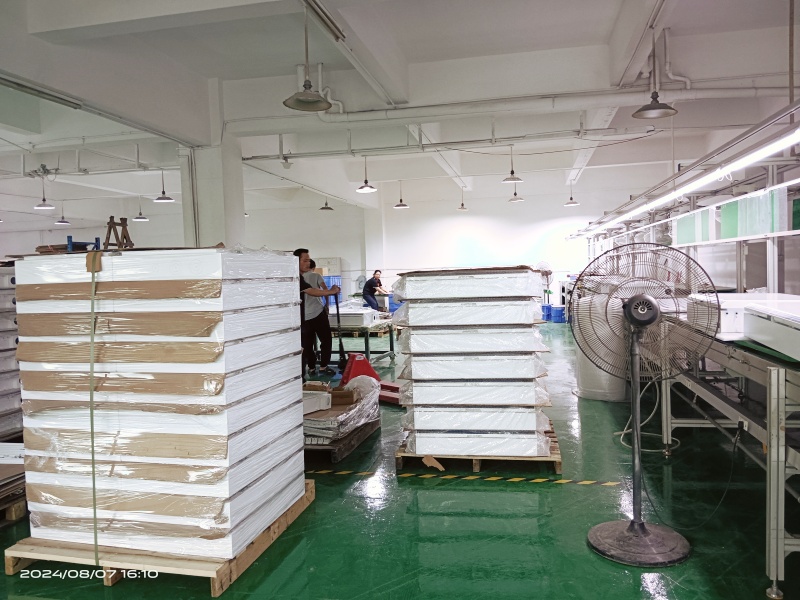
Sheet Metal Enclosure Fabrication Process
The fabrication of a sheet metal enclosure involves several steps, each requiring precision and attention to detail to ensure the final product meets design specifications. Here’s an overview of the typical fabrication process:
1. Design and Engineering
3D CAD Modeling: The process begins with creating a detailed 3D CAD model of the enclosure. This model includes all dimensions, features, and tolerances.
DFM Review: The design is reviewed for manufacturability, ensuring that it can be produced using available machinery and within budget.
2. Material Selection and Preparation
Material Choice: Based on the design requirements, the appropriate sheet metal material (e.g., aluminum, stainless steel, or mild steel) is selected.
Cutting Sheets: The metal sheets are cut to the required size using tools like shears, saws, or lasers.
3. Cutting and Punching
Laser Cutting: High-precision laser cutting is used to cut out the main profile of the enclosure from the sheet metal. This includes cutting out holes, slots, and other features.
Turret Punching: For repetitive and complex hole patterns, turret punching machines may be used. This step is crucial for creating mounting points, ventilation holes, and other features.
4. Bending/Forming
Press Brake Bending: The cut sheet is placed in a press brake machine, where it is bent into the desired shape. The bending sequence and angles are carefully controlled to achieve the exact shape specified in the design.
Roll Forming: For curved or cylindrical shapes, roll forming machines may be used. The metal is passed through a series of rollers that gradually shape it.
5. Welding and Assembly
Spot Welding: For joining two or more metal parts, spot welding is often used. This technique applies pressure and heat to weld the metal together at specific points.
TIG/MIG Welding: For more robust joints or when dealing with thicker materials, TIG (Tungsten Inert Gas) or MIG (Metal Inert Gas) welding is used.
Fastening: In cases where welding is not suitable, mechanical fasteners like screws, rivets, or nuts and bolts are used to assemble the parts.
6. Surface Treatment
Deburring: After cutting and forming, the edges of the metal may be sharp. Deburring is the process of smoothing these edges to remove burrs and ensure safety.
Surface Cleaning: The metal surface is cleaned to remove any oil, dirt, or oxidation that could affect subsequent finishing processes.
Surface Finishing: Depending on the design requirements, the enclosure may undergo various surface treatments:
Powder Coating: A powder is electrostatically applied to the metal and then cured under heat to form a durable, protective layer.
Anodizing: Commonly used for aluminum, anodizing increases corrosion resistance and allows for color finishing.
Plating: This process coats the metal with another material (e.g., zinc, nickel) to improve corrosion resistance and appearance.
Painting: If a specific color or aesthetic is required, the enclosure may be painted.
7. Machining and Tapping
Machining: Additional machining might be required to add features like threaded holes, countersinks, or precise cutouts.
Tapping: If threaded holes are needed for screws or bolts, tapping is performed to create internal threads.
8. Quality Control
Dimensional Inspection: The enclosure is inspected to ensure it meets all specified dimensions and tolerances. This may involve the use of calipers, micrometers, or coordinate measuring machines (CMMs).
Visual Inspection: Surface finish and overall appearance are checked for consistency, scratches, or other defects.
Fit and Function Tests: The enclosure is tested to ensure that it fits properly with other components and functions as intended.
9. Assembly and Integration
Component Assembly: If the enclosure is part of a larger assembly, components like gaskets, hinges, or electronic boards may be installed.
Final Assembly: The enclosure is assembled into its final form, often including the addition of covers, doors, or access panels.
10. Packaging and Shipping
Packaging: The enclosure is carefully packaged to prevent damage during transportation. Custom packaging may be used for delicate or high-value parts.
Shipping: The final product is shipped to the customer or the next stage in the manufacturing process.
11. Post-Production Support
Documentation: All necessary documentation, including inspection reports, material certifications, and assembly instructions, is prepared and provided.
After-Sales Support: Depending on the agreement, support might be provided for installation, troubleshooting, or modifications.
By following this fabrication process, you can ensure that the sheet metal enclosure is produced efficiently, meets quality standards, and is ready for its intended application.
Click sheet metal fabrication company china or china sheet metal forming manufacturers to learn more about sheet metal fabrication services.
For all your electrical enclosures from China, contact china sheet metal fabrication factory JIATONG now.
From Sheet Metal Fabrication Companies in China, china sheet metal fabrication manufacturers, china sheet metal fabrication companies – JIATONG