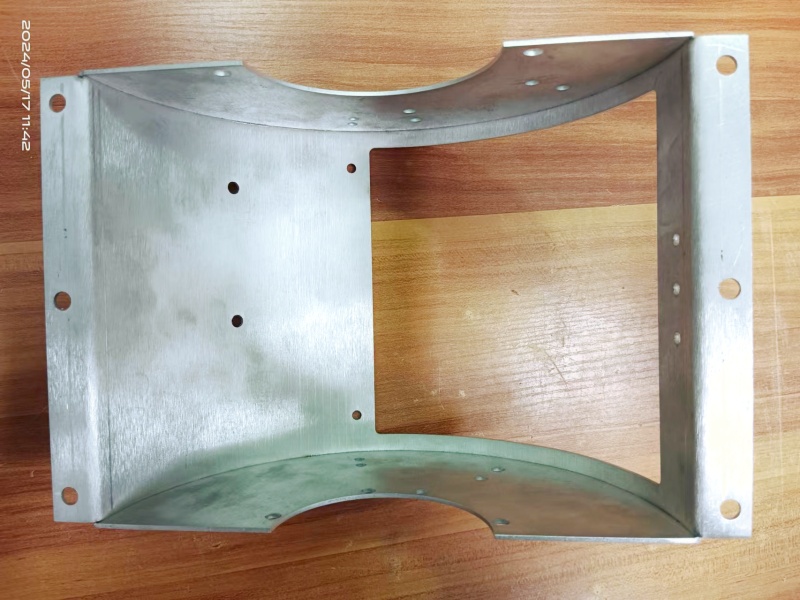
Ways to Cut Sheet Metal Fabrication Costs
1. Design Optimization
Simplify Designs: Reduce complex features that require additional cutting, forming, or welding. Fewer bends, holes, and complex shapes will reduce fabrication time and costs.
Standardize Components: Use standard sizes and shapes for parts wherever possible, reducing the need for custom tools or processes.
Optimize Material Usage: Design parts to minimize material waste. Use nesting software to optimize how parts are laid out on the sheet for cutting.
Minimize Tight Tolerances: Only specify tight tolerances where absolutely necessary, as higher precision increases machining time and costs.
2. Choose Cost-Effective Materials
Select Economical Metals: Consider using less expensive metals, such as mild steel or aluminum, instead of more expensive alloys if the application permits.
Material Thickness: Use the minimum material thickness that meets the structural and performance requirements. Thinner materials reduce material costs and cutting time.
Consider Pre-Finished Materials: Use pre-finished materials (e.g., pre-painted or anodized metals) to eliminate the need for post-fabrication finishing processes, which can save time and money.
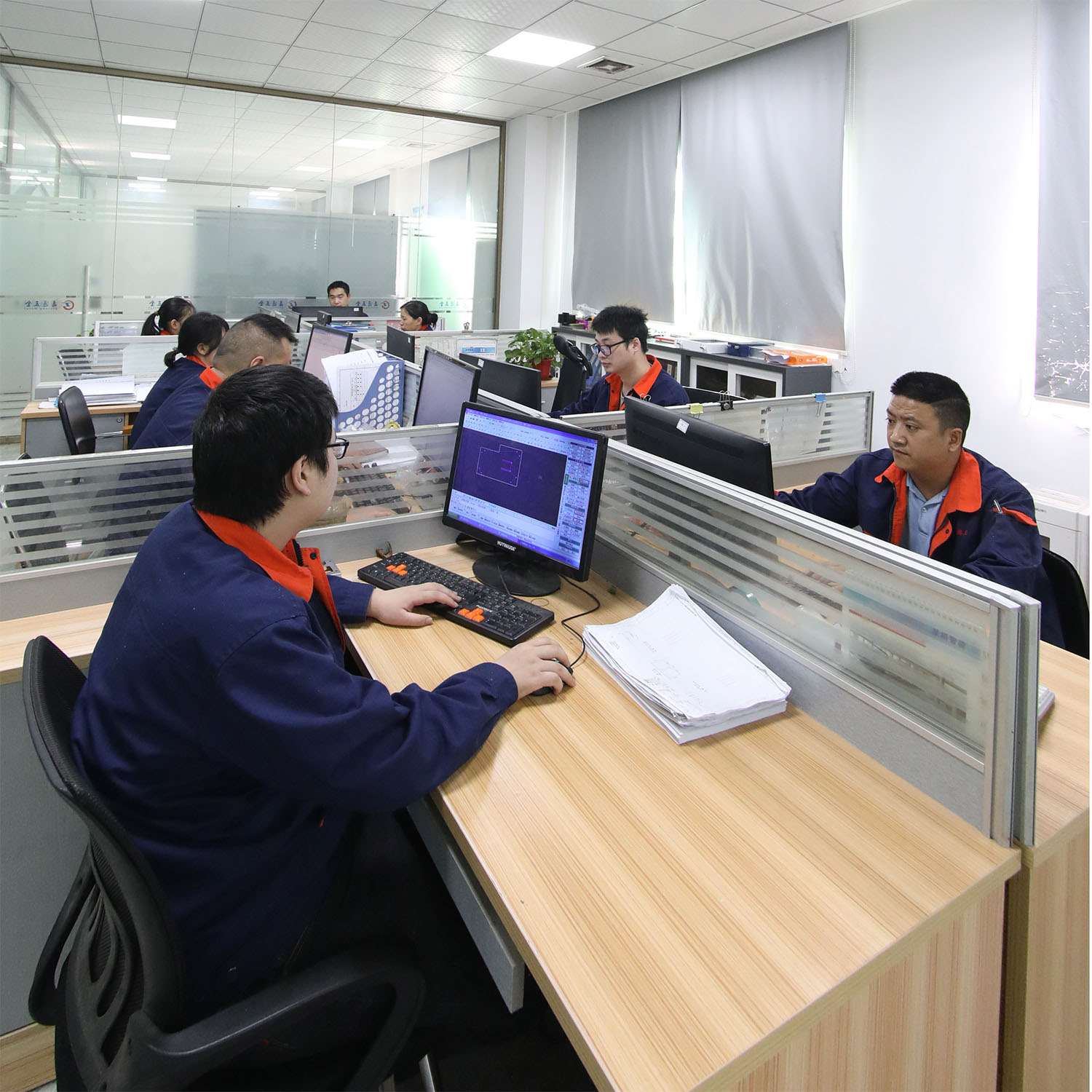
3. Leverage Efficient Manufacturing Processes
Laser Cutting or Water Jet Cutting: These methods are fast, precise, and have minimal material waste, making them more cost-effective than traditional methods like punching or shearing for complex shapes.
Automation: Use CNC-controlled machines for cutting, bending, and forming to reduce labor costs and improve efficiency. Automated production reduces errors and speeds up the manufacturing process.
Batch Production: Producing parts in larger batches reduces setup time per part and can significantly lower costs. Group similar parts together in production runs to streamline the process.
4. Outsource Smartly
Leverage Supplier Expertise: Work with experienced fabrication shops that specialize in sheet metal work. They can often suggest cost-saving design or process improvements.
Use Local Suppliers: Using local suppliers can reduce shipping costs and lead times, and allows for easier communication and collaboration.
Shop Around for Competitive Pricing: Get multiple quotes from different suppliers to ensure competitive pricing. Consider long-term partnerships that can provide volume discounts.
5. Reduce Finishing Requirements
Minimize Secondary Operations: Reduce or eliminate unnecessary finishing operations such as deburring, polishing, or coating, unless they are critical for the application.
Self-Finishing Metals: Use metals that have naturally corrosion-resistant properties (e.g., stainless steel or aluminum), eliminating the need for additional surface treatments.
6. Use Modular Design
Design for Assembly: Create modular parts that can be easily assembled with fewer fasteners or welds. This approach reduces assembly time and material costs.
Common Parts Across Designs: Reuse components across different product lines to reduce the need for different tooling and increase economies of scale.
7. Optimize Material Procurement
Buy in Bulk: Purchasing materials in bulk can lead to significant cost savings. Work with suppliers to get discounts for larger orders or longer-term contracts.
Use Remnants or Off-Cuts: Consider using remnant materials or off-cuts from previous jobs, which can be purchased at a discount and still meet your specifications.
8. Reduce Tooling Costs
Minimize Custom Tooling: Avoid custom tooling unless absolutely necessary. Standard tooling options are more affordable and have shorter lead times.
Modular Tooling: Use modular or adjustable tooling systems that can be reconfigured for different parts, reducing the need for dedicated tooling for every new design.
9. Optimize Packaging and Shipping
Design for Compact Shipping: Design parts that can be stacked or nested efficiently for shipping, reducing packaging costs and freight charges.
Flat-Pack Designs: Consider flat-pack designs that reduce shipping volume, with assembly done at the final destination.
10. Continuous Improvement
Review and Revise Processes: Continuously analyze and refine your fabrication processes to identify inefficiencies or areas where automation could reduce costs.
Employee Training: Invest in training your workforce to improve skills and reduce costly errors during fabrication.
By combining several of these strategies, you can significantly reduce the costs associated with sheet metal fabrication while maintaining quality and performance.
Click china metal enclosure manufacturers to learn more information about sheet metal fabrication services.
More Stories
What is the minimum distance between sheet metal bends?
The minimum distance between bends in sheet metal is important for maintaining the material's integrity and avoiding deformation or tearing...
What is sheet metal fabrication services?
A manufacturing process involving shaping and manipulating thin, flat sheets of metal, sheet metal fabrication is used to create different...
How do I choose sheet metal material?
Mechanical Factors Important to Sheet Metal Material Selection Strength, Ductility, Corrosion resistance, Ease of manufacture.etc Choosing the right sheet metal material involves...
What is the manufacturing industry outlook for 2025?
The global manufacturing industry is expected to experience a recovery in 2025 after a challenging 2024. Current forecasts suggest that...
How are sheet metal parts cut?
Sheet metal cutting is a fundamental step in manufacturing, where flat metal sheets are cut into specific shapes and sizes....
What type of welding wire for sheet metal?
The type of welding wire used for sheet metal depends on the welding method, material, and thickness of the sheet....