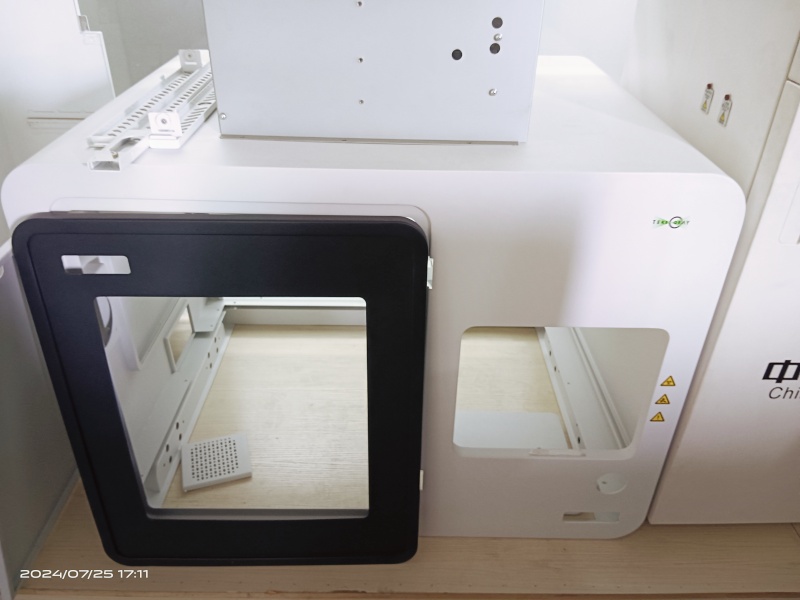
Why are metal boxes better than plastic?
Metal electrical boxes are highly durable and can withstand physical impact and environmental stress better than plastic boxes
Designing a metal enclosure involves several steps to ensure that it meets the required specifications for protection, functionality, and aesthetics. Here’s a step-by-step guide to designing a metal enclosure:
1. Define Requirements
Purpose: Determine what the enclosure will protect (e.g., electrical components, electronic devices).
Environment: Identify the environment in which the enclosure will be used (e.g., indoor, outdoor, industrial, hazardous).
Standards and Regulations: Consider the relevant standards like NEMA, IEC IP ratings, or UL that the enclosure must comply with.
2. Material Selection
Material Type: Common materials for metal enclosures include:
Steel: Strong, cost-effective, can be coated for corrosion resistance.
Stainless Steel: Highly resistant to corrosion, suitable for harsh environments.
Aluminum: Lightweight, good corrosion resistance, and easy to machine.
Thickness: Choose the appropriate thickness based on structural strength, durability, and weight requirements.
3. Determine Dimensions
Internal Space: Calculate the internal dimensions based on the size and layout of the components to be housed, including allowance for ventilation, wiring, and connectors.
External Dimensions: Consider the available space for installation and any size constraints.
Tolerance: Define dimensional tolerances for manufacturing to ensure parts fit correctly.
4. Design Layout
Component Placement: Plan the placement of internal components, considering factors like heat dissipation, accessibility, and wiring routes.
Mounting: Design internal mounting features such as brackets, rails, or standoffs to secure components.
Ventilation: Include ventilation slots, louvers, or fans if necessary to manage heat inside the enclosure.
5. Enclosure Features
Doors and Panels: Design access points such as doors, removable panels, or hinged covers for maintenance. Consider sealing options (gaskets) to maintain the enclosure’s protection level.
Sealing and Gaskets: Specify seals and gaskets to protect against dust, water, and other environmental factors.
Fasteners: Choose suitable fasteners (e.g., screws, bolts, rivets) that align with the enclosure’s material and thickness.
Locking Mechanisms: If security is a concern, design locking mechanisms for doors or panels.
6. Electrical Considerations
Grounding: Design grounding points for safety. Ensure that grounding lugs or studs are accessible.
Cable Management: Incorporate cable entry points (e.g., knockouts, grommets, cable glands) and internal cable management features like clips or ties.
7. Aesthetics and Finishing
Surface Finish: Decide on the surface finish (e.g., powder coating, anodizing, painting) to protect against corrosion, enhance appearance, and provide electrical insulation if necessary.
Color: Choose colors based on aesthetic preferences, branding, or functional needs (e.g., reflective surfaces for outdoor use).
8. Thermal Management
Heat Dissipation: Analyze heat generated by internal components and design for proper dissipation. This could involve heat sinks, ventilation, or active cooling systems.
Airflow: If using fans, design airflow paths to ensure effective cooling while maintaining the enclosure’s protection rating.
9. Prototyping and Testing
Create Prototypes: Produce a prototype or use CAD software for virtual testing. Rapid prototyping methods like laser cutting or 3D printing (for complex shapes) can be useful.
Testing: Conduct tests for fit, thermal performance, structural integrity, and compliance with protection standards (e.g., IP rating tests for dust and water ingress).
10. Manufacturing Considerations
Manufacturing Process: Decide on the manufacturing method (e.g., stamping, laser cutting, CNC machining, welding).
Tooling: Design the necessary tooling and jigs for mass production.
Cost Optimization: Evaluate manufacturing costs and optimize the design for cost-effective production while maintaining quality.
11. Documentation
Technical Drawings: Create detailed technical drawings that include dimensions, tolerances, material specifications, and assembly instructions.
Bill of Materials (BOM): List all materials, components, and hardware needed for the enclosure.
Assembly Instructions: Provide clear instructions for assembling the enclosure, including any special considerations.
12. Compliance and Certification
Regulatory Approval: Ensure that the final design complies with all necessary regulations and standards. Obtain certifications if required (e.g., UL listing, CE marking).
Labeling: Design labels for safety warnings, identification, and certification marks.
13. Production and Quality Control
Production Run: Start with a small production run to test manufacturing processes.
Quality Control: Implement quality control measures during production to ensure consistency and adherence to design specifications.
14. Final Testing
Environmental Testing: Perform environmental tests (e.g., temperature, humidity, corrosion resistance) to ensure the enclosure performs as expected.
Performance Testing: Test the enclosure under operational conditions to verify it meets all design and functional requirements.
By following these steps, you can design a metal enclosure that meets the required specifications for your application while being durable, functional, and aesthetically pleasing.
Click sheet metal fabrication company china or china sheet metal forming manufacturers to learn more about sheet metal fabrication services.
From Sheet Metal Fabrication Companies in China– JIATONG